如何在擠壓鋁型材時減少鋁材廢料?
來源:佳華 日期:2020-10-20
提高鋁型材的成品率的關鍵就是要減少和消滅廢品。廢品雖然是不可避免的,但可以設法使其降到最低。為此,可以采用如下來有效的控制和提高擠壓制品的成品率。
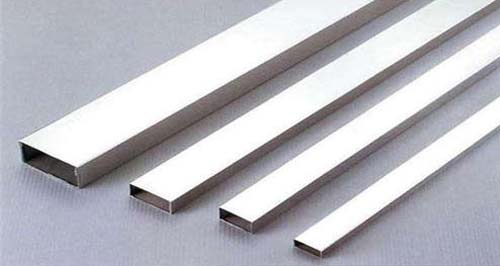
減少廢物的措施
正確選擇鋼錠長度是減少工藝浪費的主要措施。鋼錠的長度不是在擠壓前計算的,而是在擠壓之前計算出來的。
目前,大多數企業采用長棒熱切鋁棒加熱爐,與短棒加熱爐相比,鋁片損耗減少。由于模具壁厚的變化,鑄件長度的控制更加靈活、準確,成品率大大提高。然而,許多企業在使用長棒熱風爐后,忽略了鑄件長度的計算,直接將這項工作交給操作人員進行控制。操作者經常根據下桿的經驗,觀察材料的長度,如果差異較大,繼續調整,通常需要3根左右的桿才能得到精確的長度。在這一過程中,產生了大量的廢棄物,不僅降低了生產效率,而且降低了收率。
正確的方法是,在模具的初始生產中,由過程控制部門計算鋼錠的長度,當模具多次生產時,根據卡片上記錄的最后一根生產棒的長度,略微增加約5×10毫米,并在生產材料時觀察材料的長度。如果有不同的微調,使第二支棒是非常準確的.數據表明,采用長棒熱剪可以提高產量4個百分點,在實際生產中將產量提高2-3個百分點是完全可行的。
從技術水平上提高產量的措施
提高模具設計和制造水平,減少模具試驗次數是提高產品產量的一項重要技術措施。一般情況下,試驗模具成本為1×3錠,產量降低0。5%由于模具設計制造水平低,部分產品僅能生產4次以上的成品,成品率降低2≤5%,不僅造成經濟損失,而且由于反復的模具試驗,延長了生產周期。
現代模具提出了零模測試的概念,即模具制造后,不需要對模具進行測試,它可以直接應用于機器生產合格的產品。利用仿真設計軟件,進行有限元分析,可以在計算機上完成設計。通過計算機模擬,模具型腔加工在自動加工中心完成,整個模具加工是高精度完成的,所以模具質量很高,機床合格率達90%以上,可提高2≤6%的成品率。
適當提高鋁型材的擠壓系數,提高鋁的產量
每個鋁廠都有一系列的機器,每個工廠根據產品的擠壓比、冷床的長度、產品的外部部分、擠壓筒的長度和直徑來確定產品是在相應的機器上生產的。實踐證明,同一規格的產品是在不同噸位擠出機上生產的,由于擠壓系數的不同,對產品的微觀結構、性能和生產效率有很大的影響,產品的產量也會有所不同。當擠出機噸位大時,擠出系數大,產量高,擠出成本接近。
提高鑄錠質量是提高成品率的前提
鑄錠是擠壓生產的原料。鋼錠組織均勻、晶粒細小、無渣、氣孔、偏析、裂紋等缺陷,不僅降低了擠壓壓力,提高了擠壓速度,提高了產品的內在質量。并可減少表面氣泡、氣孔、劃痕、開裂、麻點等缺陷。較小的渣可以通過模具工作帶的狹縫排出,但會在型材表面造成梨痕,造成一定長度的浪費。但是,較大的渣夾雜物不會被排除在工作帶的狹縫中,導致塞模或產品開裂,模具更換,嚴重影響產品的產量。
當型材拉直時,許多企業沒有設計相應的墊片,特別是一些大型掛壁型材和空心型材,導致型材的頭、尾變形過大,當成品鋸下時,必須切斷變形部分,從而降低成品率。
墊片可以采用硬木或鋁塊,設計盡量減少墊片的規格,增加墊片的普遍性。對于懸掛墻長、截面封閉的異型材,矯直后將墊片插入密封腔時,應將支撐架放置在懸掛墻的部分。以減小長度方向的變形。夾具必須由特殊人員設計,由特殊人員管理,并由工人使用。
同時,為了防止工人們因為太麻煩而使用墊子,有必要建立與產品和工資產量掛鉤的獎懲機制。
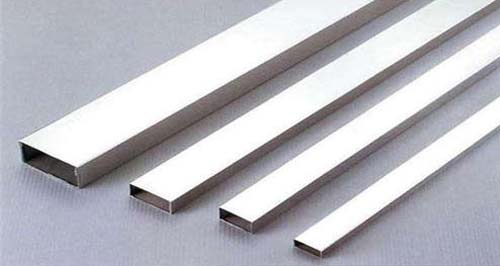
正確選擇鋼錠長度是減少工藝浪費的主要措施。鋼錠的長度不是在擠壓前計算的,而是在擠壓之前計算出來的。
目前,大多數企業采用長棒熱切鋁棒加熱爐,與短棒加熱爐相比,鋁片損耗減少。由于模具壁厚的變化,鑄件長度的控制更加靈活、準確,成品率大大提高。然而,許多企業在使用長棒熱風爐后,忽略了鑄件長度的計算,直接將這項工作交給操作人員進行控制。操作者經常根據下桿的經驗,觀察材料的長度,如果差異較大,繼續調整,通常需要3根左右的桿才能得到精確的長度。在這一過程中,產生了大量的廢棄物,不僅降低了生產效率,而且降低了收率。
正確的方法是,在模具的初始生產中,由過程控制部門計算鋼錠的長度,當模具多次生產時,根據卡片上記錄的最后一根生產棒的長度,略微增加約5×10毫米,并在生產材料時觀察材料的長度。如果有不同的微調,使第二支棒是非常準確的.數據表明,采用長棒熱剪可以提高產量4個百分點,在實際生產中將產量提高2-3個百分點是完全可行的。
從技術水平上提高產量的措施
提高模具設計和制造水平,減少模具試驗次數是提高產品產量的一項重要技術措施。一般情況下,試驗模具成本為1×3錠,產量降低0。5%由于模具設計制造水平低,部分產品僅能生產4次以上的成品,成品率降低2≤5%,不僅造成經濟損失,而且由于反復的模具試驗,延長了生產周期。
現代模具提出了零模測試的概念,即模具制造后,不需要對模具進行測試,它可以直接應用于機器生產合格的產品。利用仿真設計軟件,進行有限元分析,可以在計算機上完成設計。通過計算機模擬,模具型腔加工在自動加工中心完成,整個模具加工是高精度完成的,所以模具質量很高,機床合格率達90%以上,可提高2≤6%的成品率。
適當提高鋁型材的擠壓系數,提高鋁的產量
每個鋁廠都有一系列的機器,每個工廠根據產品的擠壓比、冷床的長度、產品的外部部分、擠壓筒的長度和直徑來確定產品是在相應的機器上生產的。實踐證明,同一規格的產品是在不同噸位擠出機上生產的,由于擠壓系數的不同,對產品的微觀結構、性能和生產效率有很大的影響,產品的產量也會有所不同。當擠出機噸位大時,擠出系數大,產量高,擠出成本接近。
提高鑄錠質量是提高成品率的前提
鑄錠是擠壓生產的原料。鋼錠組織均勻、晶粒細小、無渣、氣孔、偏析、裂紋等缺陷,不僅降低了擠壓壓力,提高了擠壓速度,提高了產品的內在質量。并可減少表面氣泡、氣孔、劃痕、開裂、麻點等缺陷。較小的渣可以通過模具工作帶的狹縫排出,但會在型材表面造成梨痕,造成一定長度的浪費。但是,較大的渣夾雜物不會被排除在工作帶的狹縫中,導致塞模或產品開裂,模具更換,嚴重影響產品的產量。
當型材拉直時,許多企業沒有設計相應的墊片,特別是一些大型掛壁型材和空心型材,導致型材的頭、尾變形過大,當成品鋸下時,必須切斷變形部分,從而降低成品率。
墊片可以采用硬木或鋁塊,設計盡量減少墊片的規格,增加墊片的普遍性。對于懸掛墻長、截面封閉的異型材,矯直后將墊片插入密封腔時,應將支撐架放置在懸掛墻的部分。以減小長度方向的變形。夾具必須由特殊人員設計,由特殊人員管理,并由工人使用。
同時,為了防止工人們因為太麻煩而使用墊子,有必要建立與產品和工資產量掛鉤的獎懲機制。